Share
Tweet
Share
Share
The automotive manufacturing sector depends on stable power distribution for smooth operations and high-quality products. This is vital for processes like assembly lines and testing. Power supply issues can disrupt these processes, causing inefficiencies and potential losses. As manufacturing systems become more advanced, focusing on power distribution details is key for meeting production goals.
Power distribution challenges are common, including unreliable power sources, overloaded circuits, and energy waste. These issues can affect productivity. To improve, it’s important to address these challenges and explore practical solutions. Factors like cable selection, energy monitoring, and system checks can play a big role in improving operations and the overall success of manufacturing. Partnering with solutions like those offered by Track Busway can further enhance flexibility and efficiency, making it easier to optimize power distribution systems.
Mitigating Power Supply Inconsistencies
Equipment malfunctions and production downtimes are caused by an inconsistent power supply. Power fluctuations can interrupt assembly lines and stop essential processes, leading to delays and higher costs. To reduce the risks of unreliable electricity, manufacturers benefit from investing in reliable power sources. Backup generators and uninterruptible power supplies (UPS) help maintain operations during outages or power issues.
Regular maintenance checks help prevent unexpected disruptions. Checking the condition of power sources, wiring, and other infrastructure can catch potential problems before they become major issues. Keeping an eye on these components reduces the chance of unplanned outages, helping the manufacturing process run smoothly.
Managing Circuit Overloads and Protecting Equipment
Overloaded circuits are a serious issue in automotive manufacturing, as they can lead to equipment failures or even fires. These risks can come up from factors like poor circuit design or incorrect power requirements. Regularly assessing power demands helps manufacturers create circuit layouts that can handle peak loads without sacrificing safety or performance. A well-planned system can handle demand fluctuations and prevent production disruptions.
Using circuit protection devices is essential for managing overloads. These devices can detect problems and automatically shut off the power when needed. Keeping track of energy consumption helps spot unusual patterns that may signal potential overloads. Setting up these protections not only extends equipment life but also creates a safer work environment, reducing the risk of major failures and improving efficiency in manufacturing.
Inefficient Energy Distribution
Energy distribution inefficiencies can drive up operational costs in automotive manufacturing. Poor wiring layouts often lead to energy losses, raising electricity bills and wasting resources. Badly designed circuits can reduce the flow of electricity, causing voltage drops and putting more strain on power equipment.
Transformers are key in energy management, making sure the right voltage reaches each part of the manufacturing process. When choosing transformers, factors like load needs and energy loss should be considered. Using energy management systems helps analyze power consumption and spot inefficiencies.
Poor Cable Selection
Choosing the right cable is key to maintaining efficiency and safety in automotive manufacturing. Selecting the wrong cable can lead to power losses and safety risks, affecting productivity and employee well-being. Important factors like voltage rating, current capacity, and environmental conditions need to be carefully considered to avoid problems caused by poor cable performance. Cables that aren’t rated properly may overheat, causing equipment failures or even fires.
An informed procurement team can greatly reduce the risk of choosing the wrong cable. Ongoing training keeps teams updated on the latest cable technologies, including improvements in insulation and design, helping them make optimal choices for automotive manufacturing.
Why Monitoring Systems Matter in Power Distribution
Lack of monitoring systems can cause serious problems in automotive manufacturing, especially with power distribution. Without real-time tracking, manufacturers may miss key energy use issues, leaving them open to inefficiencies that could be caught and fixed. Unnoticed fluctuations can lead to bigger operational problems, affecting both performance and safety.
Advanced monitoring systems solve these problems by constantly collecting data on power distribution. These systems help spot discrepancies right away, allowing managers to act quickly if something goes wrong. This technology improves operational stability and reduces the risks of power disruptions.
Addressing common power distribution challenges in automotive manufacturing is key to maintaining efficiency, safety, and product quality. By focusing on reliable power sources, well-designed circuits, efficient energy distribution, proper cable selection, and advanced monitoring systems, manufacturers can reduce disruptions and lower operational costs. Regular maintenance and proactive checks also help prevent unexpected issues that could stop production. As manufacturing advances, adopting these solutions allows companies to improve their processes, support new technologies, and create safer, more productive environments. These improvements lead to greater stability and long-term success.
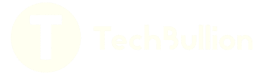