Share
Tweet
Share
Share
In today’s highly developed modern industrial automation field, the perfect combination of programmable logic controller (PLC) and servo positioning system is like a golden key to open the door to efficient and precise production, and has become one of the indispensable key technologies. This article, by Robin, the founder of MAC, a well-known CNC busbar machine manufacturer, takes everyone to deeply discuss the innovative application of PLC servo positioning system in CNC busbar punching and shearing machine, comprehensively analyzes its technical advantages and the excellent results achieved in practical applications, in order to provide a valuable reference for research and application in related fields.
- Overview of PLC and servo positioning system
PLC, as a digital computing operation electronic system specially designed for harsh industrial environments, occupies a leading position in the field of electrical equipment control with its outstanding features such as high reliability, extreme flexibility and ease of programming. An important position. The servo positioning system is composed of core components such as servo drives, servo motors, and feedback devices (such as encoders), which can accurately achieve high-precision position control. When PLC and servo positioning systems are combined, they can achieve precise motion control with ease in complex and changeable industrial control environments, fully meeting the urgent needs of modern manufacturing for efficient and precise processing.
1.1 Advantages of PLC
High Reliability: PLC adopts a variety of advanced anti-interference measures, such as hardware filtering, software anti-interference algorithms, etc., which can operate in harsh industrial environments, such as high temperature, high humidity, strong electromagnetic interference, etc. Long-term stable operation ensures the continuity and stability of the production process.
Flexibility: PLC realizes the modification and expansion of control logic through software programming, and has extremely high adaptability. Whether it is simple logic control or complex sequence control, process control, etc., PLC can easily handle it. When the production process changes or the equipment needs to be upgraded, the PLC program only needs to be adjusted accordingly. There is no need to replace hardware equipment on a large scale, which greatly reduces the enterprise’s transformation costs and time costs.
Easy to program and maintain: PLC uses intuitive and easy-to-understand programming languages such as ladder diagrams and function block diagrams. These programming languages are similar to traditional relay control circuits and are easy for technicians to quickly master and use. At the same time, PLC has a self-diagnosis function that can monitor its own operating status in real time. Once a fault occurs, it can prompt fault information in time, allowing technicians to quickly locate and solve problems, greatly shortening maintenance time and improving equipment utilization.
1.2 Characteristics of servo positioning system
High Precision: Micron-level positioning accuracy can be achieved through high-precision encoders and other feedback devices. This gives the servo positioning system unparalleled advantages in the field of precision processing, such as semiconductor manufacturing, busbar processing and other industries with high precision requirements. It plays a vital role.
Quick Response: The servo system has extremely fast response capabilities and can respond to instructions and complete corresponding actions in a very short time. This is very important for occasions that require high-speed processing, such as high-speed punching machines, CNC busbar punching and shearing machine, etc. The fast response of the servo system can greatly improve production efficiency and reduce processing time.
Good stability: The servo system has the function of automatically adjusting parameters. It can automatically adjust its own control parameters according to different working environments and working conditions to maintain a stable operating state. Even under large load changes or harsh working environments, the servo system can maintain good performance to ensure processing quality and stability of the production process.
- Technical requirements of CNC busbar punching and shearing machine
CNC busbar punching and shearing machine is an indispensable key equipment in power equipment manufacturing, mainly used for punching and shearing of busbars. Its technical requirements mainly include the following aspects:
2.1 High-precision processing
As an important conductive component in power equipment, the processing accuracy of busbar is directly related to the reliability and safety of electrical connection. The punching and shearing position of busbar must be accurate, otherwise it may lead to serious consequences such as poor electrical contact and short circuit. Traditional mechanical punching and shearing machines have been difficult to meet the strict requirements of modern power equipment for accuracy due to their complex structure, low precision, and difficult debugging. Therefore, high-precision processing technology has become an inevitable trend in the development of CNC busbar punching and shearing machines.
2.2 High-efficiency production
The power equipment manufacturing industry is highly competitive, and enterprises are facing huge production pressure and market challenges. Improving production efficiency and reducing production costs are one of the core needs for the survival and development of enterprises. CNC busbar punching and shearing machines need to have fast and stable processing capabilities, be able to complete a large number of processing tasks in a short time, reduce production cycles, and increase output. At the same time, efficient production can also reduce energy consumption and material consumption, further reduce production costs, and improve the economic benefits of the enterprise.
2.3 Flexibility and Scalability
With the continuous changes in the specifications and models of power equipment, market demand is becoming increasingly diversified. CNC busbar punching and shearing machines need to have a high degree of flexibility and scalability to meet the processing needs of different products. Flexibility is mainly reflected in the ability of the equipment to quickly adjust processing parameters and processes to adapt to the processing of busbars of different sizes, shapes, and materials. Scalability means that the equipment can easily add new functions or improve performance through simple modular and scalable design to meet higher-level processing needs that may arise in the future.
- Innovative application of PLC servo positioning system in CNC busbar punching and shearing machine
3.1 Realization of high-precision processing:
Through the close combination of PLC and servo positioning system, CNC busbar punching and shearing machine can achieve micron-level positioning accuracy. MAC CNC busbar punching and shearing machine adopts German Beckhoff PLC system and German Rexroth servo motor. After tens of thousands of debugging and iterative optimization by MAC technical engineer team, the servo system can move to the specified position quickly and accurately according to the precise instructions issued by PLC, and feedback the position information in real time through high-precision encoder to ensure the processing accuracy. During the punching and shearing process of busbar, PLC can accurately control the start, stop, acceleration and deceleration of servo motor according to the preset processing program to ensure the accuracy of punching and shearing position. At the same time, PLC can also adjust and compensate the servo system in real time according to the feedback position information to further improve the processing accuracy.
3.2 Improvement of production efficiency:
PLC’s efficient control logic and the servo system’s rapid response capability can achieve up to 150 impacts per minute, allowing the punching and shearing machine to complete processing tasks in a very short time. PLC can optimize and coordinate multiple processing procedures, realize multi-axis linkage, and further improve production efficiency. For example, during the busbar punching process, PLC can control multiple servo motors at the same time to achieve synchronous processing of multiple punching positions, greatly shortening the processing time. At the same time, PLC can also monitor the operating status of the equipment in real time, promptly discover and handle abnormal situations, avoid production interruptions, and ensure the continuity and stability of the production process.
3.3 Enhanced flexibility and scalability:
PLC realizes the modification and expansion of control logic through software programming. When the processing requirements change, only the corresponding program needs to be modified, without large-scale hardware transformation. This flexibility enables the CNC busbar punching and shearing machine to quickly adapt to the processing requirements of different products, improving the utilization rate of the equipment and the flexibility of the production line. For example, when processing busbars of different specifications, it is only necessary to modify the corresponding processing parameters and programs in the PLC without replacing or adjusting the hardware equipment. In addition, by adding or replacing servo drives and motors, the system’s functions and performance can be easily expanded to meet higher-level processing requirements that may arise in the future.
Application effect
As a CNC busbar machine manufacturer, the MAC technical team innovatively applied the PLC servo positioning system to the CNC busbar punching and shearing machine, which not only greatly improved the processing accuracy and production efficiency, but also significantly enhanced the flexibility and scalability of the system. , which has brought significant economic benefits to busbar manufacturing enterprises. With the continuous development of intelligent manufacturing and Industry 4.0, the combination of PLC and servo positioning systems will be widely used in more fields, providing strong technical support for the transformation and upgrading of the power industry.
Practical applications show that after adopting the PLC servo positioning system, the processing accuracy of the CNC busbar punching and shearing machine has increased by more than 30%, and the production efficiency has increased by more than 20%. This has enabled busbar processing enterprises to achieve significant improvements in product quality and production efficiency, and their competitiveness has been further strengthened. At the same time, the failure rate of the system has been significantly reduced, and maintenance costs have been effectively controlled, saving enterprises a lot of maintenance costs and downtime, and improving equipment utilization and production line stability.
Conclusion
In summary, the innovative application of PLC’s servo positioning system on CNC busbar punching and shearing machines has brought significant technological improvements and economic benefits to the power equipment manufacturing industry, and has broad application prospects and development potential. With the continuous advancement and innovation of science and technology, the combination of PLC and servo positioning system will continue to play an important role in promoting the development of manufacturing industry to a higher level.
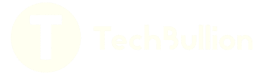
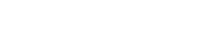