Share
Tweet
Share
Share
Warehousing plays a critical role in the supply chain. It connects manufacturers, retailers, and consumers. The introduction of advanced tools has made it very easy to manage inventory. However, despite technological advancements, many warehouses still rely on manual processes. It creates inefficiencies and errors.
Managing operations without a warehouse management system can lead to poor order fulfillment and operational congestion. In this article, we will explore the chaotic consequences of running a warehouse without a WMS system and highlight the importance of adopting modern solutions for streamlined operations.
The Chaos of Manual Warehouse Management Without WMS
Inventory Inaccuracies
Without a software system, warehouses rely on manual inventory tracking, which is prone to errors. Items can be misplaced or undercounted due to human mistakes. These inaccuracies can result in overstocking. It wastes valuable storage space and ties up capital, leading to missed sales opportunities.
Manual record-keeping lacks real-time updates and delays in inventory visibility. The resulting discrepancies can disrupt reordering schedules and leave your businesses unprepared for sudden spikes in demand. A WMS mitigates these issues by providing real-time updates, barcode scanning, and automated record-keeping.
Inefficient Order Fulfillment
Manual order processing can significantly slow down fulfillment operations. Picking and packing orders without a WMS often involve outdated, paper-based systems that are inefficient and prone to errors. Workers may pick the wrong items or quantities which can result in incorrect deliveries.
The process also lacks prioritization, causing delays for urgent orders. Inefficient fulfillment impacts customer satisfaction, as late or incorrect deliveries damage the company’s reputation. A WMS optimizes the process by automating picking routes, integrating with shipping carriers, and ensuring order accuracy. It ultimately improves speed and reduces errors in order fulfillment.
Lack of Real-Time Visibility
Manual warehouse operations lack real-time data visibility. It makes it challenging to track inventory levels, monitor workflows, or identify bottlenecks. Managers often rely on periodic physical counts, which may not reflect current inventory status. This lack of visibility can lead to poor decision-making.
Moreover, identifying and resolving operational issues becomes more difficult without timely data. A WMS system provides real-time insights into every aspect of the warehouse. It enables you to make informed decisions and improve overall efficiency. Without it, warehouses remain reactive rather than proactive.
High Labor Costs
Manual processes demand a larger workforce to handle tasks such as inventory counts, order picking, and paperwork. This reliance on labor not only increases operational costs but also leads to worker fatigue. It results in more errors and reduced productivity.
Seasonal spikes in demand further strain the workforce, as hiring and training additional staff take time and resources. A WMS automates repetitive tasks, such as inventory management and order processing, reducing the need for manual labor.
This will not only cut costs but also allow your staff to focus on strategic and value-added activities. It ultimately improves overall operational efficiency.
Slow Receiving Process
Receiving and putting away goods manually is a time-consuming process. Workers often lack clear instructions for sorting and storing items. It leads to misplaced goods and delays in making inventory available for orders. This creates bottlenecks at the receiving end and slows down the whole operation.
A WMS streamlines these processes by automating receiving workflows and assigning optimal storage locations for each item. By reducing manual intervention, a WMS ensures that goods are processed quickly and accurately. It improves overall productivity and eliminates delays caused by inefficient receiving processes.
Ineffective Demand Forecasting
As a business owner, you always want to understand and fulfill your customers’ requirements accurately. To do so, you need to forecast their demands and maintain inventory accordingly. Accurate demand forecasting is essential for efficient inventory management.
However, manual systems lack the tools to predict future requirements. Forecasting with outdated or incomplete data often results in overstocking or stockouts. Overstocking occupies space. Meanwhile, stockouts disrupt the supply chain and cause lost sales.
A WMS uses historical data, seasonal trends, and real-time analytics to provide accurate demand forecasts. By understanding future requirements, you can optimize inventory levels, reduce waste, and meet customer demand more effectively. Without a WMS, your team will struggle to maintain balance.
The aforementioned chaos highlights the importance of investing in a robust WMS system. If you want to avoid them, make sure you get a reliable system and implement it properly.
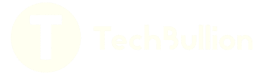