Share
Tweet
Share
Share
In the complex world of industrial automation, the precision of motion control is paramount. At the heart of this precision lies the servo drive controller, a pivotal component that governs the performance of servo systems used across various applications, from robotics to assembly lines. This article delves into the functionalities, benefits, and applications of servo drive controllers in industrial automation, offering insights into their integral role in enhancing operational efficiency and productivity.
Understanding Servo Drive Controllers
Servo drive controllers are sophisticated devices designed to precisely control the motion of servo motors. They are part of a closed-loop system that includes the servo motor and feedback devices, such as encoders or resolvers. The primary function of a servo drive controller is to receive command signals from a central control system or operator, process these signals, and regulate the power sent to the servo motor to achieve the desired motion.
Key Functionalities:
- Command Interpretation: Servo drive controllers interpret input commands that dictate the desired position, speed, or torque of the servo motor.
- Signal Amplification: They amplify the low-power command signals to levels sufficient to drive the motor.
- Feedback Processing: By receiving feedback from the motor about its actual state, servo drive controllers adjust the output dynamically to correct any deviations from the intended motion.
Components of Servo Drive Controllers
Understanding the components of servo drive controllers provides deeper insight into their complexity and functionality:
- Power Amplifier: Converts low-power input signals into high-power output signals that drive the motor.
- Microcontroller: The brain of the controller, which executes software algorithms to control and monitor the servo system.
- Interface: Allows for communication between the servo drive controller and other components of the automation system, as well as for user interaction for settings and adjustments.
- Feedback Mechanisms: Integral sensors provide real-time data back to the controller to ensure accuracy and precision in motor control.
Advantages of Using Servo Drive Controllers in Industrial Automation
The integration of servo drive controllers into industrial systems offers numerous advantages:
- Enhanced Precision and Accuracy: The ability to precisely control the motion of servo motors is crucial in applications requiring exact movements, such as in CNC machining or robotic assembly. The high-resolution feedback and sophisticated control algorithms enable exact positioning and movement.
- Improved Productivity: Faster response times and the ability to execute complex motion patterns seamlessly translate into higher throughput and more efficient production processes.
- Reduced Mechanical Stress: By regulating acceleration and deceleration, servo drive controllers help in reducing mechanical wear and tear on equipment, thereby extending the machinery’s life.
- Energy Efficiency: Servo drive controllers optimize the power usage of motors, reducing energy consumption by ensuring that motors operate only at required levels of power and performance.
- Flexibility: Modern servo drive controllers are highly programmable, offering flexibility to adapt to different tasks and changes in production specifications without needing significant hardware changes.
Applications in Various Industries
Servo drive controllers find applications in numerous industries due to their versatility and efficiency:
- Manufacturing: They control robotic arms used in assembly lines, ensuring precise placement and movement.
- Automotive: Used in automated systems for assembling complex components like transmissions and engines.
- Consumer Electronics: Essential in the production lines for devices requiring high precision like smartphones and tablets, where they manage the machinery that assembles minute electronic components.
- Packaging: Servo drive controllers manage the operations of machinery involved in the high-speed packaging of goods, adjusting the movements for a variety of package sizes and shapes.
- Aerospace: They control the automated systems used in the manufacturing of aircraft components, where precision and reliability are critical.
Challenges and Considerations
Despite their benefits, integrating servo drive controllers into industrial systems presents challenges:
- Complexity in Setup and Maintenance: The advanced nature of servo drive controllers requires specialized knowledge for installation, configuration, and maintenance.
- Cost: The initial investment for high-quality servo drive controllers can be significant, though it is often offset by gains in efficiency and productivity.
- Integration with Existing Systems: Ensuring compatibility between new servo drive controllers and existing industrial infrastructure can require additional resources and careful planning.
Future Trends
The future of servo drive controllers like the iDKC03.1-040-7-FW n industrial automation looks promising, with ongoing advancements in digital technology and artificial intelligence. Predictive maintenance, enhanced real-time data analytics, and further improvements in energy efficiency are areas likely to see significant development. Additionally, the integration of IoT devices and cloud technology could enable more sophisticated and interconnected control systems.
Conclusion
Servo drive controllers are indispensable in modern industrial automation, offering unmatched precision, control, and efficiency. As industries continue to push the boundaries of what is possible in manufacturing and production, the role of servo drive controllers will undoubtedly expand, driving innovations that reshape how industries operate and thrive in an automated world.
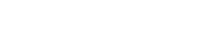