Share
Tweet
Share
Share
Waiting for a halted machine can be frustrating. One fact stands out: expertise in production line installation services is key. This article shows ways to keep your line moving, with less waiting.
Read on, it’s helpful.
Understanding Production Line Installation
Setting up a production line involves many parts, like machines and software. It usually takes weeks to months to get everything working right.
Key components involved
Production line installations need custom steel and stainless-steel parts. These components are crucial for building strong structures. Bulk material handling systems move goods quickly through the production line.
Piping fabrication ensures that liquids flow where they should. Finally, fitting industrial equipment into place is a big part of the setup.
Each piece plays a vital role in automation and logistical flow, avoiding downtime caused by logistical obstacles or lack of maintenance. Next up, understanding how to put it all together within a typical timeframe helps keep projects on track.
Typical timeframe for installation
Moving on to the typical timeframe for installation, the duration can vary, but here’s a straightforward outline.
Project Stage | Timeframe |
Planning & Design | 2-4 weeks |
Procurement of Materials | 4-6 weeks |
Installation | 6-12 weeks |
Testing & Commissioning | 2-4 weeks |
Total | 14-26 weeks |
This schedule indicates projects can take 14-26 weeks to complete. Timeframes may adjust depending on the project’s scope and intricacy. Maintain project timelines with expert assistance and appropriate tools.
For instance, SJEC completes turnkey projects effectively, assuring on-time and cost-effective deliveries. The Lost World of Tambun Water Slide project exemplifies their ability to handle complex tasks proficiently.
Strategies to Minimize Downtime
Planning is key to reducing downtime. Use simulations before installation. Modular parts can speed up the process too. Schedule work during quiet times—this helps keep production running smoothly…
You’ll save time and money by thinking ahead!
Pre-installation planning and simulation
Pre-installation planning helps cut downtime. Simulation tests setups before they are in place.
- Define clear goals. Write down what you want to achieve during installation. Make sure everyone understands these goals.
- Use free UAV surveys for assessments. Drones can help spot challenges early on, which saves time and money later.
- Create a detailed timeline for each phase of the process. This lets teams know when to start and finish their parts.
- Involve key people early in discussions. Getting input from engineers, operators, and logistics staff ensures all viewpoints matter.
- Run simulations of the production line setup before installations begin. Testing different scenarios helps identify potential issues that could arise during real operations.
- Ensure compliance with industry standards from day one. Sticking to these rules avoids costly delays or rework down the road.
- Plan for preventative maintenance schedules once installation is complete. Setting this up now can prevent future breakdowns.
This careful planning leads seamlessly into utilizing modular components for easier upgrades…
Utilizing modular components
Modular components can help cut down downtime during production line installations. They make the process faster and easier.
- Quick Replacement
Modular parts allow for quick upgrades or repairs. You can change out a section without affecting the whole system. - Customized Design
These components come in various sizes and functions. This lets you tailor your setup to fit your specific needs. - Simplified Installation
Modular systems are easier to install than traditional ones. You can build them in parts, which saves time on-site. - Future Upgrades
Using modular parts means future upgrades are more straightforward. It’s easy to add new technology as it becomes available. - Reduced Waste
Modular designs often use materials efficiently, which is eco-friendly. This aligns with sustainable practices that many companies now seek. - Cost-Effective Solutions
Although they can seem expensive at first, modular components save money over time due to reduced labor costs and less downtime. - Compatibility with Tech Tools
Many modular systems work well with automated tools for installation and monitoring, ensuring a smooth operation.
Using modular components helps keep production lines running smoothly while minimizing disruptions, especially in packaging operations.
Scheduling installations during off-peak hours
Scheduling installations during off-peak hours makes a big difference. This strategy helps reduce downtime. Work often slows down in the evenings or on weekends. Fewer people on-site means less distraction and quicker tasks.
Companies can finish projects faster by planning around busy times. It also ensures safety and quality during installations. By choosing these quieter periods, teams can focus better and get the job done right.
Smart scheduling is key to keeping production running smoothly while upgrades happen efficiently.
Leveraging Technology for Efficient Upgrades
Technology can help speed up upgrades. Automated systems cut down on time. They make it easier to fit new parts into a line. Real-time monitoring tools show how work is going. This helps teams stay on track and fix problems fast…
keeping everything running smoothly.
https://www.youtube.com/watch?v=lh8pZfLoVc8
Automated systems for quicker integration
Automated systems speed up integration during production upgrades. These tools help fit new components quickly. They reduce the time workers spend on setup. With real-time data, teams can track progress easily.
This tracking helps find and fix issues right away.
Using automated systems also cuts down on human error. They ensure parts work together smoothly from the start. Companies benefit by getting back to full production faster. Advanced engineering design services support these systems, providing seamless industrial integration with specialized tools and techniques.
Real-time monitoring tools to track progress
Real-time monitoring tools keep everyone updated during production line installation. These tools provide instant updates on the project’s status. They show what tasks are done and what is left to do.
With project management cloud software, teams communicate clearly. Clients receive real-time updates too, which helps avoid delays.
Using these tools ensures that installations stay on schedule. They track progress closely and highlight any issues right away. This way, teams can fix problems quickly and keep everything moving smoothly.
Importance of Professional Installation Services
Professional installation services bring expert skills to your project. They know the right tools and methods for complex setups, making sure everything runs smoothly.
Expertise in complex installations
Complex installations need expert help. With over 23 years of experience, professionals handle these tasks well. They have completed more than 900 projects successfully. Their skill covers every step of the process, from planning to execution.
This ensures all work meets strict standards and stays on schedule.
Using specialized tools and techniques makes a big difference too. Experts know how to use technology that speeds up the installation process. Their knowledge cuts down risks and helps avoid mistakes, leading to smoother operations in production lines.
Next, we will explore how leveraging technology can make upgrades more efficient.
Access to specialized tools and techniques
Specialized tools and techniques can make installation smooth. An expert team uses advanced equipment for quick setups. This ensures safety and precision during upgrades. With specialized tools, tasks get done faster, reducing downtime.
Access to these resources helps keep costs low while delivering top-notch results. These professionals come prepared with the right techniques for every challenge on the production line.
Free technical consultations help clients pick what’s best for their needs, ensuring efficient solutions from start to finish.
Conclusion
Minimizing downtime during production line installation and upgrades is crucial. Plan ahead to avoid delays. Use modular components for easier setup. Schedule work when the plant is less busy.
Trust professionals for better results – they bring skill and tools that save time. With these steps, you can keep your production moving smoothly.
FAQs
1. What does minimizing downtime during production line installation and upgrades mean?
Minimizing downtime refers to reducing the time a production line is non-operational during installations or upgrades, thus ensuring more productivity.
2. Why is it important to minimize downtime in production lines?
It’s crucial because less downtime means more operation time, leading to increased output and profits. Plus, it helps maintain workflow continuity… no unnecessary breaks!
3. How can I effectively minimize downtime during these processes?
You can do so by planning ahead… having a clear upgrade or installation plan that considers potential issues. Also, regular maintenance checks help spot problems early on.
4. Can any unforeseen situations cause extended downtimes?
Yes indeed! Equipment failure, power outages – they could all lead to extended downtimes if not planned for properly… So always have a backup plan ready!
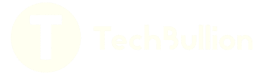