Share
Tweet
Share
Share
In the fast-paced manufacturing industry, continuous improvement and process optimization are indispensable strategies for achieving excellence and staying ahead of the competition. Defined as the incremental improvement of processes, systems, and products, continuous improvement drives efficiency and quality. Process optimization, on the other hand, focuses on making operations as effective and useful as possible. Together, these approaches address inefficiencies and defects that can negatively impact product performance and a company’s bottom line.
Bhavin Patel exemplifies the power of integrating manufacturing excellence with supply chain optimization. With over six years of experience in the automotive and medical device industries, Bhavin is currently a Quality Engineer at Edwards Lifesciences in Draper, Utah. In this role, he applies Lean Manufacturing and Six Sigma principles to streamline processes, ensure supplier quality compliance, and drive operational efficiency. His expertise includes leading Material Review Board activities, managing supplier quality initiatives, and conducting validations to maintain adherence to FDA and ISO standards.
Previously, Bhavin served as a Quality Engineer at Becton, Dickinson and Company (BD), where he successfully implemented standardized inspection processes and optimized material flow, resulting in significant productivity improvements. Throughout his career, Bhavin has consistently demonstrated commitment to data-driven strategies and innovative problem-solving, driving lasting improvements in quality and efficiency across manufacturing and supply chain functions.
Path to Lean and Six Sigma
Bhavin’s journey into Lean Manufacturing and Six Sigma began during his time in the automotive industry at BYD, where precision and efficiency were essential. He witnessed how even minor process inefficiencies could significantly impact production and quality, which sparked his interest in finding structured methods for improvement. “I was particularly drawn to Lean and Six Sigma because they offered a practical, data-driven approach to identifying and eliminating waste, reducing variation, and enhancing overall process capability,” Bhavin shares.
His background in Mechanical Engineering further reinforced his focus on continuous improvement. The engineering mindset of optimizing designs and developing innovative solutions naturally aligned with the principles of Lean and Six Sigma. At BYD, he applied these methodologies to streamline workflows, minimize waste, and elevate product quality. The success of these efforts not only validated his approach but solidified his belief in the transformative power of continuous improvement—a commitment he has carried throughout his career.
Fixing backlogs with CAPA
At BD, Bhavin spearheaded a CAPA initiative to address a significant backlog of over 7,000 repaired notifications that remained open in the system despite the repairs being completed. This data integrity issue disrupted the ability to track repair metrics accurately, necessitating immediate action. Bhavin assembled a cross-functional team from IT, quality, service, and manufacturing to identify the root cause. Their investigation revealed that insufficient access permissions within the SAP system were preventing the automatic closure of completed notifications. “This created a significant data integrity issue and hampered our ability to accurately track repair metrics,” Bhavin explains.
To resolve the issue, the team collaborated with IT to adjust access permissions, enabling the system to close notifications automatically and drastically reduce the backlog. Beyond the immediate fix, Bhavin implemented preventive measures by revising internal processes for managing SAP user access, introducing stricter controls, and conducting regular audits. This comprehensive approach not only resolved the backlog but also streamlined workflows and improved reporting accuracy. It underscored the critical role of robust process management and system controls in maintaining operational efficiency and data integrity.
Optimizing processes with data
The importance of data as the foundation for effective process optimization is a key principle emphasized by Bhavin. His approach to KPI analysis begins with clearly defining objectives and identifying the most relevant metrics, ensuring that efforts are focused on areas that truly impact performance. Once the right KPIs are established, he meticulously gathers accurate and reliable data from various sources. Using statistical tools, Bhavin analyzes the data for trends, patterns, and anomalies, transforming raw information into actionable insights.
At BD, this method proved invaluable when analyzing repair notification data. Bhavin identified an unusually high number of notifications related to a specific component in one product line. “Further investigation revealed that this component was experiencing premature wear due to a minor design flaw,” he explains. By addressing the issue with a design change, the team not only reduced repair notifications but also improved product reliability and customer satisfaction. This experience reinforced Bhavin’s belief in the power of data-driven decision-making to uncover inefficiencies and drive impactful improvements.
Mastering ISO compliance
Leading ISO audits demand a structured and methodical approach to identifying and addressing non-conformances while ensuring sustainable compliance. Bhavin begins this process by thoroughly reviewing audit findings and documenting each issue with clarity. He collaborates with relevant teams to conduct in-depth root cause analyses using tools like 5 Whys and fishbone diagrams. “It’s crucial to involve the people directly involved in the processes, as they often have the best insights,” Bhavin notes, emphasizing the value of frontline expertise in uncovering underlying issues.
To ensure lasting improvements, Bhavin goes beyond immediate fixes. He revises procedures, updates documentation, provides targeted training, and establishes robust controls to embed changes into the system. Effectiveness is verified through follow-up audits and ongoing monitoring, creating a closed-loop system that prioritizes sustainability. “This closed-loop system of identifying, correcting, preventing, and verifying ensures that improvements are not only implemented but also sustained over time,” he explains. This meticulous approach not only maintains compliance but also fosters continuous improvement across processes.
Root cause solutions that last
Effective defect reduction hinges on a structured and collaborative approach to root cause analysis, a principle Bhavin applies consistently. His process begins by clearly defining the problem and assembling a cross-functional team with the necessary expertise. At BD, Bhavin tackled a significant issue involving over 7,000 repaired notifications that remained open in the system. The team gathered comprehensive data, including system logs, user access records, and process documentation, to investigate the issue. Using tools like the 5 Whys, they discovered the root cause: insufficient access permissions within SAP, which prevented automatic notification closures.
Once the root cause was identified, Bhavin’s team implemented corrective and preventive actions (CAPA). The immediate solution involved updating SAP access permissions to resolve the backlog, while long-term measures included revising internal processes for managing user access and instituting regular audits. Bhavin explains, “This closed-loop approach, from investigation to implementation and verification, ensures that the solutions are not only effective in addressing the immediate problem but also prevent future occurrences.” By monitoring notification closure rates after the changes, the team confirmed the success of their efforts, demonstrating the lasting impact of systematic root cause analysis.
Tools for continuous improvement
Lean Manufacturing tools like FMEA, 5S, and 8D are integral to Bhavin’s process optimization strategy, each serving a unique purpose tailored to specific challenges. FMEA (Failure Mode and Effects Analysis) is central to proactive risk assessment, helping to identify potential failure modes during design and development phases and enabling the implementation of preventive measures early on. For workplace organization, 5S (Sort, Set in Order, Shine, Standardize, Sustain) plays a critical role in eliminating inefficiencies such as unnecessary motion and time spent searching, ultimately enhancing safety and efficiency.
When addressing complex problems, Bhavin relies on the 8D (Eight Disciplines) problem-solving methodology to develop structured corrective actions. “When choosing the right tool, I consider the nature of the problem,” he explains. FMEA is his choice for preventing issues, 5S for improving workplace organization, and 8D for tackling intricate challenges requiring a disciplined approach. By leveraging the strengths of these tools, Bhavin ensures continuous improvement and consistently achieves optimal results in his efforts to enhance manufacturing processes.
Building a culture of progress
Motivating and aligning diverse teams to embrace process changes is a challenge Bhavin addresses with a thoughtful and multifaceted approach. Clear communication and transparency are at the heart of his strategy. He ensures all teams understand the “why” behind the changes, emphasizing the benefits not just for the organization but also for their individual roles. “It’s crucial to show how these changes will make their work easier, more efficient, or improve product quality,” Bhavin explains.
By actively involving team representatives in planning and implementation, Bhavin fosters a sense of ownership and draws on their expertise to refine processes. Adequate training and support further build confidence and ease the transition to new workflows. Recognizing and celebrating successes, no matter how small, reinforces positive behavior and maintains momentum. Through this combination of communication, collaboration, and recognition, Bhavin effectively drives alignment and cultivates a culture of continuous improvement across all functions.
Redefining quality inspections
During his time at BYD, Bhavin led a transformative initiative to streamline the incoming inspection process, which had become a bottleneck causing production delays and potential quality issues. To address this inefficiency, he assembled a cross-functional team of inspectors, engineers, and quality assurance professionals to conduct a thorough analysis. This involved observing workflows, analyzing inspection data, and gathering input from inspectors to pinpoint bottlenecks and areas for improvement.
A significant challenge Bhavin faced was resistance to change from some inspectors, who feared the new methods might increase their workload. To overcome this, he highlighted the long-term benefits of the new process, including reduced inspection time, greater accuracy, and improved work-life balance. Actively involving the inspectors in the redesign and implementation ensured their input was valued, fostering ownership of the changes. The result was a significant reduction in inspection time, enhanced product quality, and a notable boost in team morale. This project underscored Bhavin’s commitment to active listening, clear communication, and collaborative problem-solving as drivers of successful change.
Bhavin’s expertise in process optimization and continuous improvement has helped him achieve impressive results throughout his career, and his commitment to these principles continues to drive success in his current role. Manufacturing companies that embrace these concepts and methodologies can gain a significant competitive advantage, ensuring they remain leaders in their respective industries.
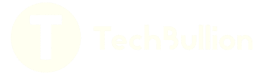